Introduction
In the realms of biotechnology and pharmaceuticals, making an informed decision while choosing a monoclonal antibodies manufacturer is paramount. A wrong choice could compromise the quality, efficacy, and safety of the produced antibodies, thereby impacting therapeutic outcomes and research validity. This guide aims to assist in navigating through the crucial aspects of selecting the right manufacturer.
Molecule Fit and Process Development, Setting the Foundation for Success
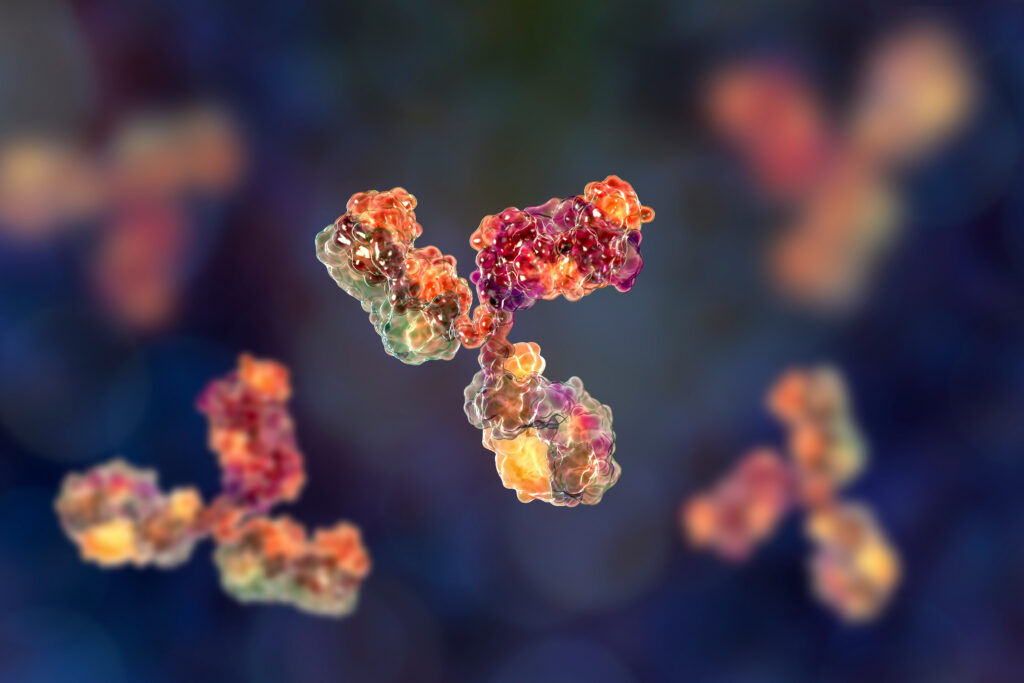
Learn more about how “Choosing the Right Biologics CDMO for Your Therapeutic Development Needs”
Make Sure it’s a Molecule Fit
First choosing a monoclonal antibody CDMO with experience in your specific monoclonal antibody type whether it be an IgG, IgA, or IgM is essential. Specialization can translate into optimized production processes, enhanced product quality, and quicker development times, thereby reducing the time-to-market. A CDMO with expertise in your specific molecule type is likely to have encountered, and overcome, many of the common and rare issues related to the production of such antibodies, ensuring a smoother, more predictable collaboration and outcome.
Ensure a Robust and Reproducible Process
Identifying a monoclonal antibodies manufacturer that exhibits competence in formulating robust and reproducible processes from the client’s cell line is paramount. The ability to develop these solid processes is crucial as it drastically minimizes risks associated with variability and errors throughout the antibody production phase. A manufacturer with such capabilities will adhere to stringent quality controls and operational precision, ensuring the generation of consistent and high-quality monoclonal antibodies. This level of reliability and reproducibility not only facilitates optimal research and development conditions but also ensures the resulting antibodies are dependable for therapeutic applications, thus maximizing the potential for successful clinical outcomes. It signifies the manufacturer’s commitment to excellence and their understanding of the sophisticated nature of monoclonal antibody production, which is essential in advancing medical science and patient care.
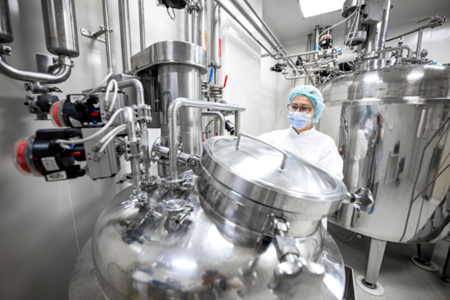
Scalable to GMP Quantities for Later Stage and Commercial Manufacturing
It’s imperative for monoclonal antibody manufacturers to furnish scalable processes capable of producing Good Manufacturing Practice (GMP) quantities, spanning between 100 to 2000L, a requirement pivotal for advancing to subsequent stages and for commercial manufacturing. This scalability provided by the monoclonal antibodies manufacturer is not merely a matter of production volume but is also critical to the adaptability and flexibility of the production process, allowing for adjustments in production scales in response to market demands or project requirements. Furthermore, this approach is crucial to maintaining lower long-term costs of goods sold (COGS), ensuring that the monetary aspects are streamlined and that the end products can be made available at competitive prices, ultimately benefiting the consumer base and contributing to the manufacturer’s market position.
Proper Characterization with Monoclonal Antibody Manufacturers
Analytical methods to ensure safety, purity, and efficacy
The selected manufacturer should qualify analytical methods during the drug development process before entering clinical trials to guarantee the safety, purity, and efficacy of the drug candidates during manufacturing.
Transferable Analytical Methods to the QC Department
Selecting a manufacturer who meticulously qualifies analytical methods during the drug development process is essential before progressing to clinical trials. This stage is a cornerstone in guaranteeing the safety, purity, and efficacy of the drug candidates during the entire span of manufacturing. The qualification of analytical methods serves as a rigorous verification system, ensuring each drug candidate meets the predefined quality parameters and is free from detrimental impurities. It not only acts as a gatekeeper to clinical trials but also as a continual assurance mechanism throughout the manufacturing process.
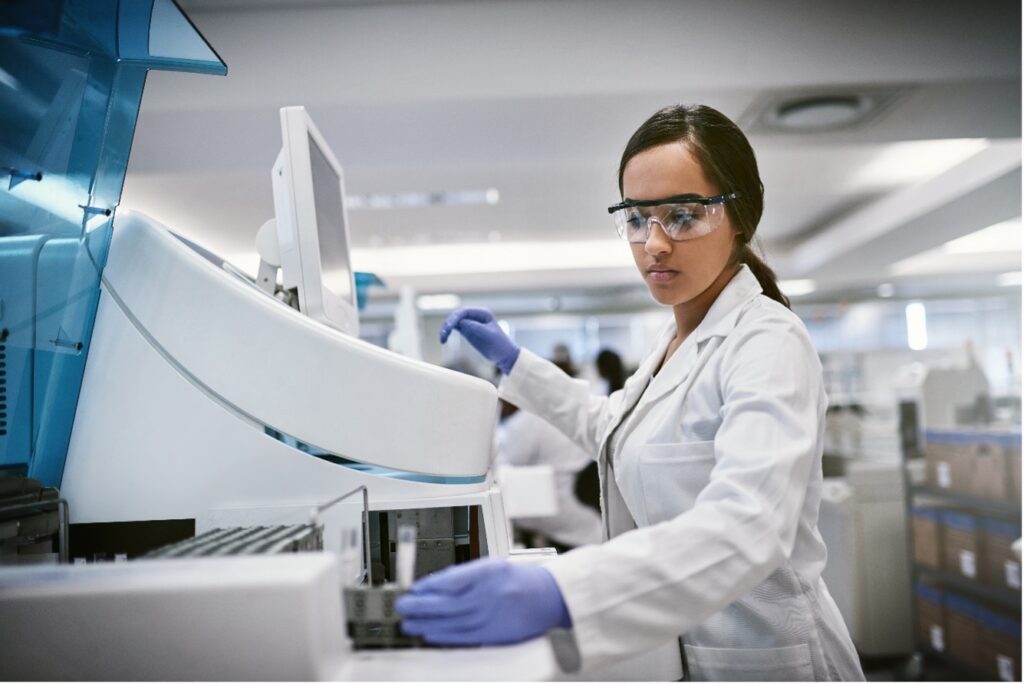
Stability of Monoclonal Antibody Drug Substance and Drug Product
When choosing a monoclonal antibodies manufacturer, it’s imperative that they can substantiate the prolonged stability of your monoclonal antibody drug substance and the finished drug product. A reputable Contract Development and Manufacturing Organization (CDMO) should ideally be equipped with in-house stability chambers, capable of managing a spectrum of temperatures including -70C, 2-8C, and 25-37C, to ensure the integrity and viability of the products. This capability is crucial, as it not only underscores the CDMO’s commitment to quality and excellence but also guarantees the reliability and efficacy of the monoclonal antibodies in various conditions.
Final Step of Fill-Finish with a Monoclonal Antibodies Manufacturer
Importance of In-House Fill Finish
The drug product fill and finish into primary packaging represent one of the final and most critical stages in monoclonal antibody production. It is pivotal to choose a monoclonal antibodies manufacturer that possesses in-house fill finish capabilities to significantly mitigate the risk of contamination. By doing so, it ensures the preservation of the drug substance and prevents the loss of substantial amounts, maintaining the overall integrity and quality of the final product.
Minimizing Risks in the Supply Chain
Transferring drug substance to a different facility for converting it into a drug product can introduce several unwarranted risks, primarily associated with the demands of cold chain shipping and storage. To circumvent these risks, partnering with a monoclonal antibodies manufacturer adept in managing the entire supply chain seamlessly is vital. This ensures not only the quality and integrity of the drug substance but also the efficacy and reliability of the final product, minimizing potential losses during the production process.
mAb Developers and Differentiated Packaging
mAb developers are showing a growing preference for monoclonal antibody manufacturers capable of providing diverse packaging options such as vials, syringes, and cartridges to accommodate various administration routes. Consequently, selecting a Contract Development and Manufacturing Organization (CDMO) that has the flexibility to fill the specific vessel required for your chosen administration route becomes crucial. This choice is paramount as it ensures the adaptability of the packaging process to the unique needs of the product, enhancing its applicability and accessibility.
Summary and Conclusion
Choosing the right monoclonal antibodies manufacturer is an intricate and crucial process, requiring careful consideration of various factors including process development, antibody characterization, and the final steps of fill-finish. Ensure that the selected manufacturer meets industry standards, employs robust and reproducible processes, offers scalable solutions, and can effectively manage the supply chain. By meticulously evaluating potential manufacturers based on these factors, you can secure a partner who will contribute significantly to the success of your monoclonal antibody project.
Talk to us about Your Biologics Project
Need a monoclonal antibodies manufacturer? GBI is a one-stop shop that can take your project from Drug substance to Drug Product all under one roof! Contact GBI Biomanufacturing today.
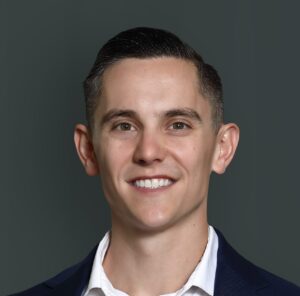
Nick has a track record of developing partnerships with pharmaceutical and biotechnology executives to support the biologic CMC activities required to support their clinical trials and hit development milestones. With a background as a bench scientist specializing in manufacturing scale-ups, Nick brings a unique skillset that bridges the business and technical communications between GBI’s team and external stakeholders. Nick’s recent experience involved business development roles for Tokyo Chemical Industry and Cytovance Biologics. He has a B.S. in chemistry and an MBA from the University of Massachusetts, Lowell.