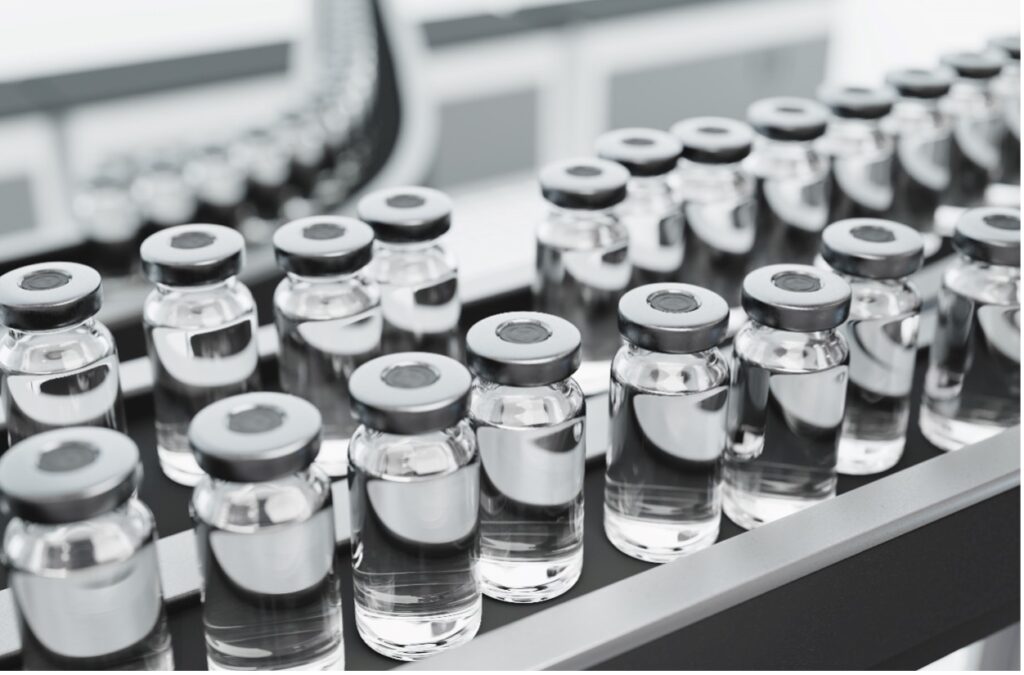
Introduction
In the ever-evolving landscape of biomanufacturing, sterile fill finish plays a pivotal role in ensuring the safety and efficacy of biopharmaceutical products, especially biologics and sterile injectables. This critical phase in the production process involves the aseptic filling of biologics into vials or other containers, followed by the sealing and finishing steps. As the demand for these specialized services continues to grow, Contract Development and Manufacturing Organizations (CDMOs) are at the forefront of innovation, driving advancements in aseptic liquid filling and sterile vial filling technologies. This article explores the current state of sterile fill finish technology and its future trends, shedding light on the innovations and developments that are shaping the industry.
Evolution of Sterile Fill Finish Technology
Historical Perspective
To understand the future, it’s crucial to appreciate the journey so far. The evolution of sterile fill finish technology has been marked by milestones, from traditional aseptic techniques to the state-of-the-art methods employed today. Sterile fill finish is a crucial step in pharmaceutical manufacturing, ensuring that biologics and sterile injectables maintain their integrity and quality. This process involves aseptic liquid filling, which requires precision and stringent adherence to regulatory guidelines. The CDMOs specializing in sterile fill finish play a vital role in helping pharmaceutical companies navigate the complexities of this critical manufacturing stage.
Sterile Fill Finish for Biologics
Biologics present unique challenges in terms of stability and sensitivity. CDMOs are tailoring sterile fill finish processes to accommodate the specific needs of biologic products, ensuring both safety and efficacy. Biologics, with their complex structures and delicate nature, demand specialized handling during the manufacturing process. Sterile fill finish for biologics requires advanced technology and expertise to preserve the potency of these therapeutic agents. Leading CDMOs in this space are continually investing in innovative solutions to cater to the unique challenges posed by biologics.
Learn more about “How Sterile Fill Finish Techniques Ensure Drug Integrity and Patient Safety” here!
Single-use Systems
The shift towards single-use systems is gaining momentum in the biomanufacturing industry. The advantages of disposable technologies in sterile fill finish are it contributes to operational flexibility, reduced risk of cross-contamination, quicker changeover times and cost-effectiveness. Keep in mind there is an anticipation of potential changes to the regulatory landscape that may impact the industry with all the new advances and equipment’s emerging.
Global Market Trends
Market Trends and Dynamics
Understanding the current market trends is crucial for staying ahead in the sterile fill finish arena. The market dynamics, include mergers and acquisitions, regulatory landscape, and the influence of global events on the sterile fill finish market. Tailoring equipment to meet the rise of personalized medicine brings forth new challenges for sterile fill finish technology. CDMOs are adapting to the unique requirements of personalized medicine, including smaller batch sizes and specialized formulations, while maintaining the highest standards of sterility. This also promotes continuous manufacturing, which is gaining traction across the biopharmaceutical industry, offering advantages in terms of efficiency and quality control.
Environmental Monitoring and Control
Ensuring the sterility of the fill finish process is of up most importance. In the era of sustainability, the pharmaceutical industry is placing greater emphasis on environmentally conscious practices. To consider environmental monitoring, CDMOs are incorporating green initiatives into their aseptic liquid filling processes, from eco-friendly packaging materials to energy-efficient manufacturing facilities. The use of Process Analytical Technology (PAT) tools, including real-time monitoring and feedback systems, provides continuous process verification and optimization to improve process understanding, control and efficiency.
Collaborations and Partnerships
Collaborations between CDMOs and pharmaceutical companies are driving innovation for sterile fill finish. There have been many successful partnerships that have resulted in groundbreaking developments in this space. The success of sterile fill finish operations heavily relies on the capabilities of the CDMO overseeing the process. Choosing the right sterile fill finish partner is critical for pharmaceutical companies aiming to bring their products to market efficiently and in compliance with regulatory standards.
Learn more about “Choosing the Right Biologics CDMO for your Therapeutic Development Needs” here!
Emerging Technologies in Sterile Fill Finish
Next Generation Fill Finish Equipment
These flexible manufacturing platforms are designed to be more versatile and adaptable to various container formats, volumes and product types. The integration of smart technologies is enhancing efficiency and improving overall product quality. Having the ability to switch between different products and configurations with minimal downtime will allow for the CDMO industry to easily manufacture for the growing demand of vialed drug products.
Automation and Robotics
Advancements in automation and robotics are revolutionizing sterile fill finish equipment. From vial loading to stoppering, advanced robotics are streamlining and enhancing the efficiency of the fill finish line. The role of automation is mainly to reduce human interventions, minimize contamination risks, and optimize production speed. Robotics Systems can be employed for tasks such as vial handling, cap placement, and inspection.
Click here to read more about market growth, single-use systems, pre-filled syringes, automation and investing in Aseptic Fill Finish Manufacturing capacity!
Novel Aseptic Techniques
Aseptic liquid filling and aseptic vial filling are critical aspects of sterile fill finish. Emerging aseptic techniques that aim to enhance the sterility assurance level during the fill finish process will positively impact the industry. From isolator technology to restricted access barrier systems (RABS), these innovations contribute to maintaining product integrity, safety and compliance with regulatory standards. These in-line monitoring and control systems will further improve the aseptic processing environment as well.
Conclusion
In conclusion, the future of sterile fill finish technology is marked by innovation, and adaptability. The industry is witnessing a shift towards advanced technologies that not only meet current challenges but also anticipate and address future needs. As we move forward, aseptic liquid filling, automation, and environmental considerations will continue to shape the landscape of sterile fill finish, with a focus on personalized medicine and adherence to evolving regulatory standards. As biopharmaceutical companies continue to invest in biologics and sterile injectables, staying abreast of these trends is imperative for achieving success in the competitive biomanufacturing landscape. The journey toward safer, more efficient sterile fill finish processes is an exciting path that promises to revolutionize the production of biologics and sterile injectables.
Talk to us about Your Sterile Fill Finish Projects
Need Drug Product? GBI is a one-stop shop that can take your project from Drug substance to Drug Product all under one roof! Contact GBI Biomanufacturing today!
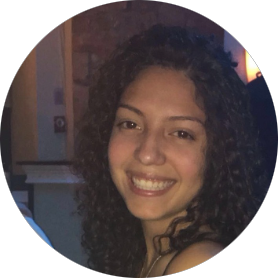
Yaslin is a dynamic and accomplished professional whose background is in Pharmaceutical Sciences with preclinical expression of drug transporters and its impact on chemical disposition and toxicity. Currently she has been focusing her years of invaluable experience in the biotechnology industry starting with Research and Development work at Assembly Biosciences. Yaslin has showcased her versatility by making significant contributions to the marketing and sales industry, working for Seacret Direct before transitioning to her current role at GBI Biomanufacturing. Fluent in both English and Spanish, she combines linguistic dexterity with a detail-oriented, engaging and determined approach to every task. With a BS in Pharmaceutical Sciences and MBA from the University of Rhode Island, she seamlessly bridges the worlds of science and business together.