As the global regulatory landscape continues to evolve towards increased stringency, technology transfer of biopharmaceutical manufacturing programs continues to elevate. By focusing on the importance of smart, efficient and in process-oriented approaches moving into new or different facilities can ensuring a smooth transition that leverages best practices and innovative solutions.
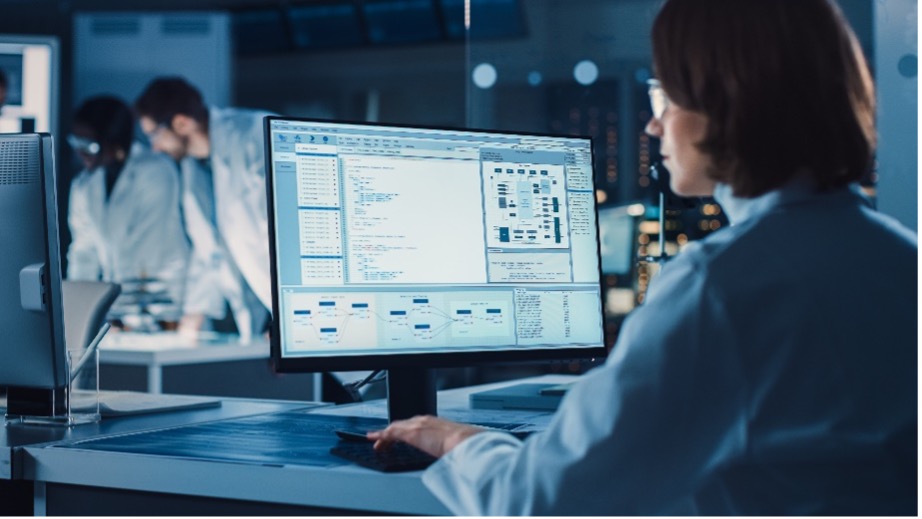
GBI Biomanufacturing relies on proficient mechanisms to transfer programs in from early development through the different clinical phases within the CMC continuum such as from pre-clinical, to clinical stage production and finally late stage preparing for PPQ and commercial manufacturing.
We employ a formalized process to bring in the manufacturing processes of protein therapeutics from different facilities and different scales to adapt and optimize that process to our technologies.
This tech transfer activity can occur several times during a product lifespan as it emerges from the development lab through commercial manufacturing. GBI can handle these programs coming in at any stage/phase, after early development through commercial.
In our experience the technology transfer process occurs for the following reasons, and we have supported our clients for each of those.
- First is the transition from a “Eureka” moment to preparation for first in human studies. Here we analyze the processes employed at the development lab, understanding what could transition well to a cGMP environment and what will need re-development. We review and understand the molecule so that we can build a process that maintains the integrity of the protein in manufacturing, rather than trying to repair later with formulation manipulations. As well as, how to best fit or optimize into a platform manufacturing process recognizing we will apply customization when necessary.
- When there is a need for scale-up, in which the current facility cannot meet that technology demand or lack of capacity at current manufacturing location or provider. We review the process to determine if it is adaptable from say 5liter scale directly to 200 liters or greater. There are times where intermediary scale-up runs may be required, which will depend on data developed at small-scale production and an understanding of the protein’s key quality attributes. In other situations, for example, will a 200-liter process need to scale to 2,000 liters due to phase advances, increased demand for ethical use, or expanded indications?
- Beyond approval, programs may be transferred to companies acquiring the technology to second source providers.
At GBI we have a rigorous process for technology transfer. The first step is information download. We ensure that our team has the experience and expertise in the areas that will be functionally transferred, by understanding the key parameters of the incoming program.
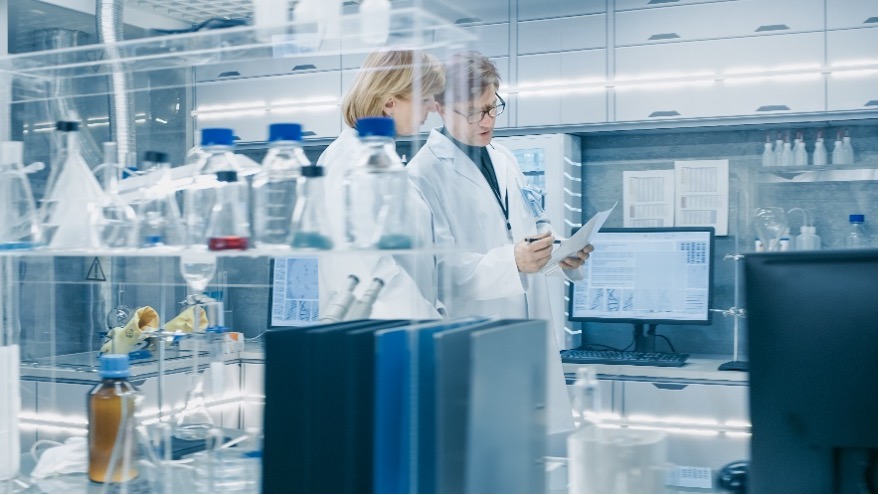
Learn more about “Overcoming Scalability in Biologics: CDMO Strategies for success” HERE!
We’ll analyze the equipment used in the originating facility and understand the differences compared to our facility, in order to identify areas where process changes may be needed.
And all components, consumables, and raw materials would be reviewed to ensure compatibility or substitution.
And as a part of the information transfer, we will understand the critical process steps and if there are indications that optimization is needed. Also, in some instances, the entire process may need to be reworked or a seamless transfer can occur. All these possibilities are analyzed and documented.
GBI will also undertake a risk assessment for the project transfer, seeking to understand risks associated with quality parameters, the timeline for transfer, ultimate manufacturing of the GMP batch(es), any risks in regulatory compliance, and the risk associated with the process itself based on full review of previous manufacturing parameters.
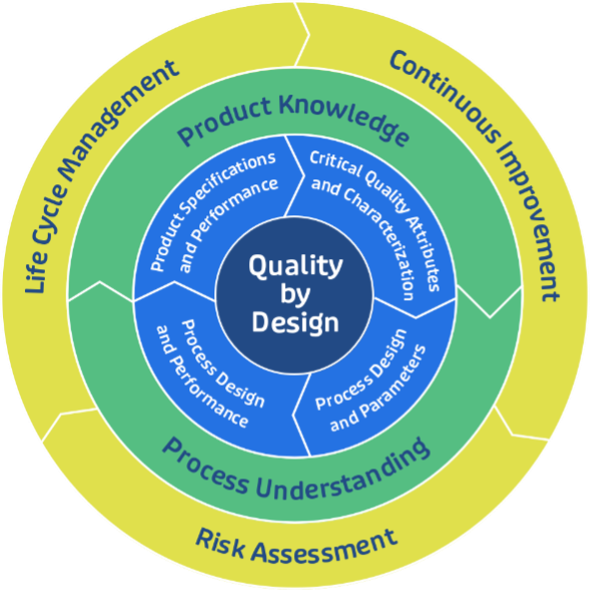
Once the knowledge base is established GBI and the client are now ready for project kickoff which includes introduce the teams, lay the groundwork and rules for interactions set the program timelines and objectives to work together through the tech transfer into GMP manufacturing. This will include gap analysis based upon understanding the process on paper and our approach to transfer-in, trying to identify areas where key details are missing or unidentified and then determine a plan for those elements.
GBI has transferred in many programs at various stages. The transfer involves our process development and GMP manufacturing experts, working together to ensure the scale down models will translate readily to the selected GMP scale-up. At the same time the analytical methods transfer will be layered in with our QC/QA teams to ensure that all assays are ready, validated and robust.
Typically, an engineering run at scale is performed. This “confirmation” of the upstream activity can also be performed at smaller scale, if review of the process demonstrates that risk of multi-fold scale up is minimal. The engineering run is an opportunity to focus on process parameters that may create product related issues and shake out any questions about the scale up to the final GMP scale. Downstream process parameters are followed rigorously through final bulk drug substance fill.
When complete, pre-GMP production activities and the analytical assays are ready, cGMP production is the next step and of course the ultimate objective of the tech transfer. All of the work and effort that preceded the GMP run is evident in the GBI approach, as we meet our commitments to clients to achieve ahigh quality product (and process) for the patient receiving the drug.
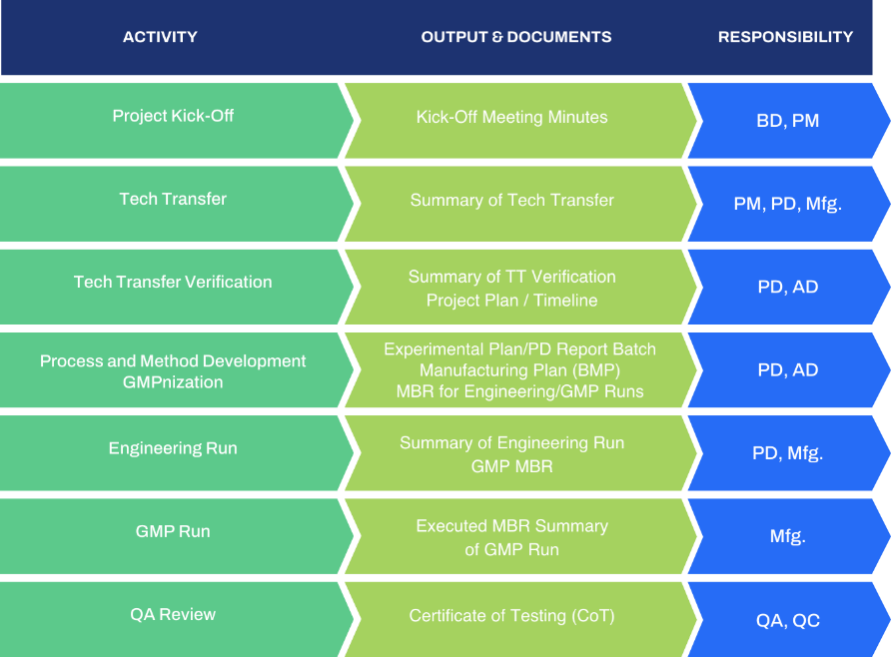
In summary, at GBI we strive to implement a robust tech transfer by paying strict attention to:
- Documents and Information transfer
- Clear communication of objectives, timelines, budgets, and deliverables
- Introducing teams for the manufacturing partner and the client sponsor – roles and responsibilities
- The Scope of Work plan detailing the processes
- Demonstrating a confirmation of the process via the Engineering run and excellence in the adherence to the specified steps for the cGMP run.
GBI Biomanufacturing has been successful manufacturing our client programs by following these important steps and philosophies. Now if and when things happen as sometimes it does in the biologics manufacturing world, the culture is understanding and performing actions to identify solutions to issues that arise, communication of the plans, action to right-set the process and stay on track for our clients’ patients.
Need an experienced CDMO with a seamless tech transfer process for Biologics? GBI is a one-stop shop that can take your project from Drug substance to Drug Product all under one roof! Contact GBI Biomanufacturing today.